Air conditioning systems and ventilation technology: design perfection for logistics halls
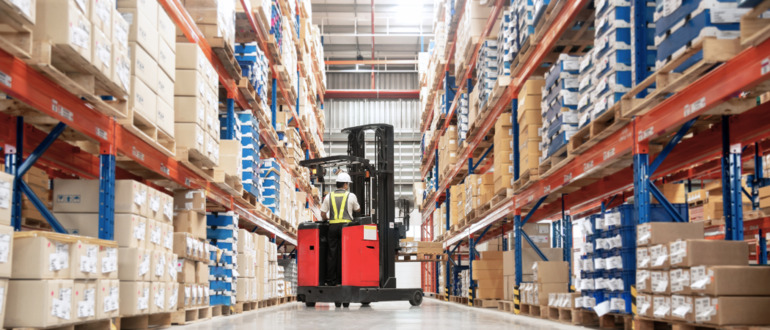
Air conditioning systems and ventilation technology: design perfection for logistics halls
When it comes to designing ventilation and air-conditioning systems for logistics halls, the basic principles of flow mechanics always apply – regardless of the specific requirements for the hall temperature.
- Blog
- End customer - Investor
Advantages of torsion air distributors
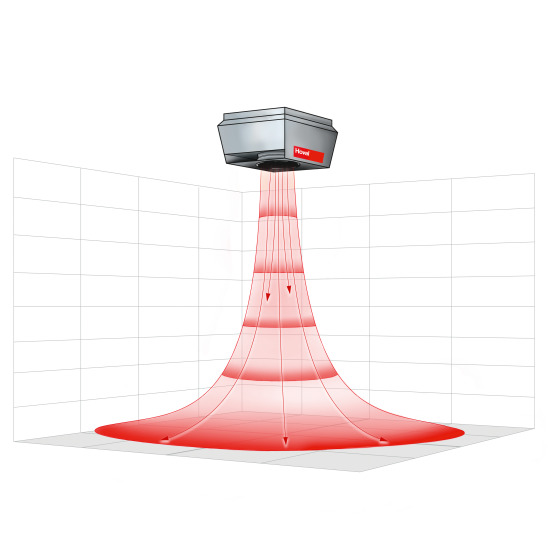
In heating mode, a highly concentrated air stream is emitted at high speed from the distributor and a negative pressure difference occurs around the air columner. As a result, the ambient air moves from the ceiling area and, to a lesser extent, from the top shelves towards the air stream. As the depth of penetration increases, the air stream slows down, the surrounding negative pressure decreases and the ambient air is induced. The flow then reaches the bottom shelves.
In order for the flow to pass efficiently to the next shelves, a space of 0.2 to 0.3 metres (m) should be left between the floor and the shelving. The improved air distribution makes it possible to optimise the flow of up to three aisles with a series of air passages. (Refer to Fig. 1: Air flow through aisles.)
Rows of shelves restrict the rotationally symmetrical flow of torsion air distributors. The fronts of the rows of shelves act as walls as far as air flow is concerned, causing wall jets to form. These have a wider reach than open jets and a greater mounting height than is the case with free flow distribution. This increase can be up to 1.5 m.
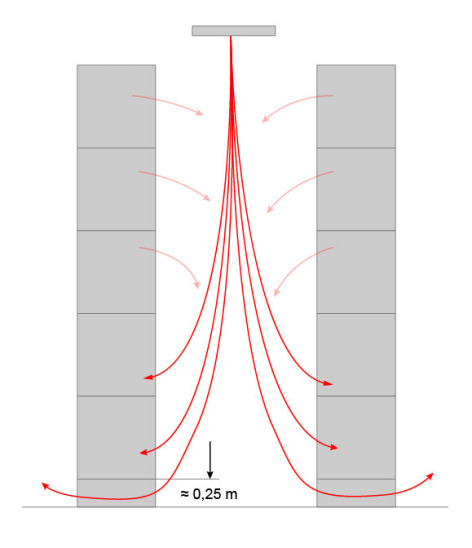
Adhering to set temperatures
Maximum permissible temperatures (upper temperature limit)
These apply, for instance, when storing food or pharmaceutical products and are usually below 25 degrees Celsius. In the case of direct application on the top shelves, the supply air temperature in heating mode may not exceed the upper temperature limit. This allows only a small temperature range and, in turn, a low heat output, meaning a relatively large number of ventilation units need to be installed to maintain the temperature.
This is where torsion air distributors come in, as they boost the temperature range and heat output. In heating mode, the air flow is strongly concentrated and there is no need to supply air directly to the top shelves. Consequently, the supply air can be blown in at a temperature of around three Kelvin (K) higher than the required upper limit temperature. The heat output required can then be achieved with fewer units, which cuts back on the initial investment and ongoing operating costs – and, of course, is good news for the environment too.
During the summer months, the set temperature limits can be maintained using recirculated or outdoor air units. Air from the outside can be used for direct and/or indirect cooling. Automated system control comes highly recommended in order to adhere strictly to these temperature limits.
If a lower and upper temperature limit need to be adhered to, the vertical temperature gradient is crucial. If, for example, goods need to be stored between 18 degrees Celsius and 21 degrees Celsius (3 K), the height of the hall must not exceed 12 m with a gradient of 0.25 K/m.
Centralised vs decentralised supply of media
Supply air and pollutant concentration
If diesel forklift trucks are used in a hall, additional country-specific technical regulations are binding. To avoid exceeding permissible pollutant concentrations, the supply air flow must be adjusted accordingly, if necessary.
Modern electric forklift trucks are powered by lithium-ion batteries. No hydrogen is released when they are being charged, which puts them at an advantage over standard lead-acid batteries. This also means that their charging stations do not need to comply with the ATEX Directive for explosion protection and prevention, and no further ventilation measures need to be taken. If shelf conveying systems are in use, the heat released by the systems needs to be taken into account when calculating the cooling load.
Learn more about Hoval Indoor Climate Systems for logistics and industrial halls